Transformation and digitalisation
In its new Development Strategy for 2022–2031, KMG places a special focus on digital transformation.
Digital transformation is the Company’s priority tool for achieving its strategic goals in the modern world. Since the launch of our Transformation Programme in 2015, we have made considerable progress in re-engineering our production and supporting business processes:
- The Company reduced the number of management levels by liquidating sub-holdings. This helped us optimise budget spending and made it possible to address day-to-day issues in a more expedient manner.
- The Company radically transformed its procurement, IT, HR, safety, and cybersecurity frameworks. It resulted in both operational achievements and financial benefits. For example, the benefits from category-based procurement were around KZT 10 bln in 2016–2020.
- Shared services centres for IT and HR management were created.
From 2015 to 2021, the benefits from implementing the Transformation Programme totalled KZT 115 bln.
In line with current trends and given the importance of digitalisation for its further development, KMG has already launched digital projects.
The first project involved the implementation of the Smart Field concept at two of our subsidiaries – Kazgermunai (KGM) and Embamunaigas (EMG). At KGM, telemechanics were introduced at key wells, centralised control systems were implemented, and two situation centres now operate (in the headquarters and at the field). All this allows real-time streamlining of processes and helps identify losses, improve equipment performance, and ensure a high level of safety.
EMG generated a digital model for seven fields. Smart control stations are in place for online detection of deviations at each well and monitoring of maintenance crews’ work.
In oil exploration and production, digitalisation is based on the ABAI information system. ABAI consolidates KMG Group’s operational information into a single database and can verify and analyse it using artificial intelligence, machine learning and instant visualisation tools.
Five system modules were launched for testing in 2021.
- ABAI Database is an in-house data import and storage system. It also generates production reports and ensures prompt access to all KMG exploration and production data.
- The Visualisation Centre module consisting of three dashboards is designed for the visualisation and monitoring of production and strategic performance indicators (for example, daily production by subsidiaries).
- The Well Operation Mode algorithms analyse the performance and calculate potentials of wells, thus ensuring more efficient distribution of planned oil production among wells and reservoirs, and, accordingly, optimising field development. The module operation is based on actual data from KMG’s own database, current and potential bottom-hole pressure and the productivity index. These values are used to calculate the maximum potential oil volumes given the existing geological and technical conditions. During the testing period from May to October 2021 alone, 560 tonnes were added to the output at 13 wells of KGM.
- The Monitoring of Process Complications module enables a tailored approach to injecting corrosion inhibitors and determining their dosage based on the actual corrosion rate at fields of OzenMunaiGas (OMG). This increases equipment reliability (due to to a higher effectiveness of the inhibitor) and reduces spending on chemicals. In about six weeks, the testing helped to save more than KZT 5 mln at three facilities.
- The Selection of Downhole Pumping Equipment module will enable more rapid and robust selection of pumps through automated data processing. The module optimises DPE, well operation, and assessment of the potential of newly drilled wells. For example, a correctly selected DPE arrangement will reduce equipment failure rates and the number of well workovers at JSC Mangistaumunaigaz (MMG) by 4%.
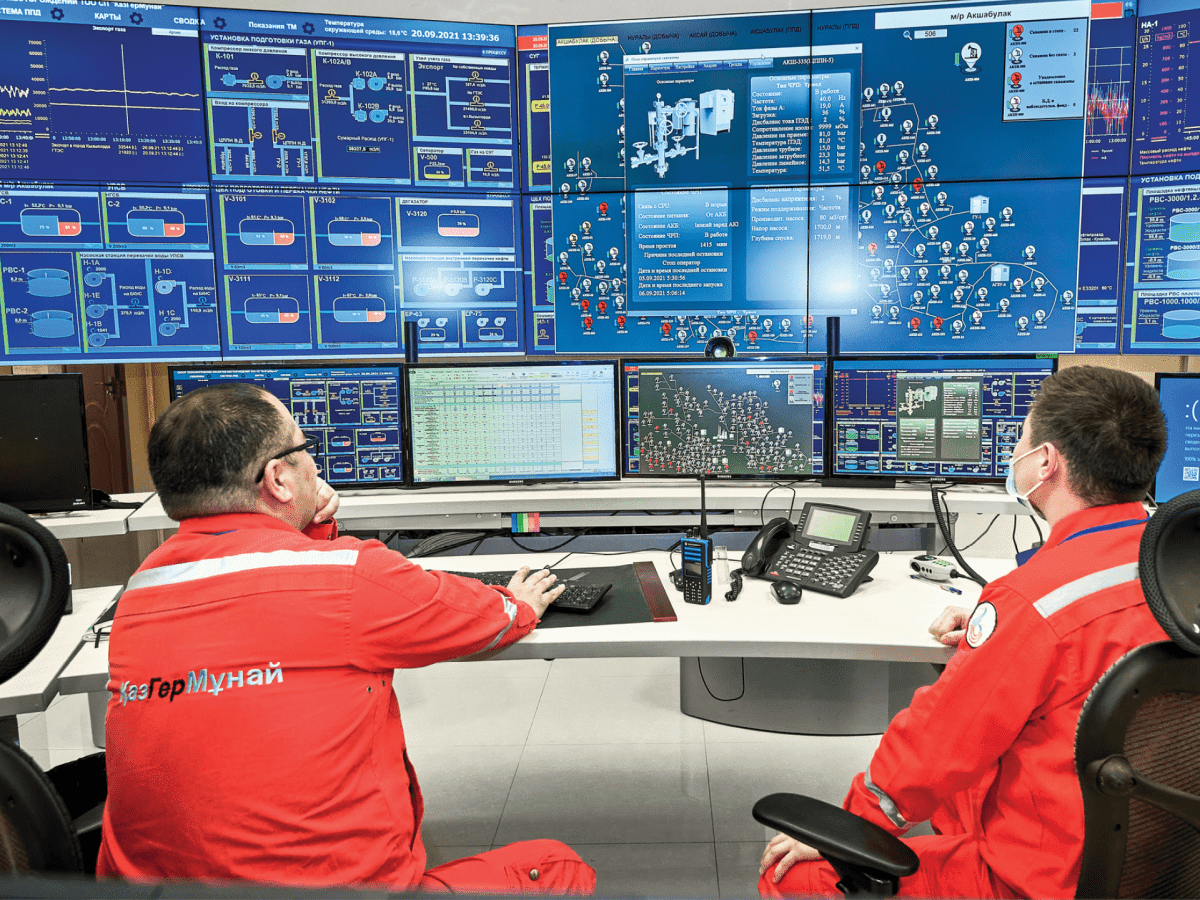
During the second project phase, twelve more ABAI modules will be developed to digitalise key oil production processes – from exploration to drilling to production to economic effect assessment.
The Transformation emphasises on enhancing digital and design skills, as well as employee motivation. So, the implementation of the Lean 6 Sigma (LSS) programme involves employee training and certification at KMG Group’s production assets. A total of 13 LSS projects were implemented in oil production, generating a benefit of KZT 72 mln.
The LSS programme was previously successfully implemented at refineries. Since 2016, 156 projects have been implemented under the programme at refineries, with a direct economic effect of KZT 1,247 mln due to lower reagent, steam and power consumption and reduced repair costs. 89 employees have been trained and certified. At the National Competition Qazaqstan Project Management Awards, the implementation of Lean 6 Sigma programme project in oil refining and petrochemistry was named Kazakhstan’s best project in 2021.
We plan to roll out the programme with a focus on digitalisation (Lean Digital). This means that LSS tools will be used to develop business initiatives aimed at reducing operational wastes by using custom digital solutions.
The implementation of the Bank of Ideas platform at MMG will facilitate the development of an innovation culture at operating assets and address critical operational issues at KMG subsidiaries, involving those who participate in the relevant processes on a daily basis.
Three KMG refineries in Kazakhstan are introducing computer simulators. Operators of refinery units use digital twins to simulate emergencies or routine operations, thus minimising process disruptions caused by human error and enhancing workplace safety.
Simulators have been launched on the delayed coker, isomerisation unit and naphtha splitter, diesel hydrotreating plant, and kerosene hydrotreater at Pavlodar Refinery, catalytic reformer at Shymkent Refinery, catalytic cracking unit, catalytic reformer, and aromatic hydrocarbon production facility at Atyrau Refinery. Such simulators are expected to cover a total of 21 units.
In 2021, the Oil Refining and Petrochemicals segment completed the creation of a digital General Plan and 3D model of refineries. All facilities were laser-scanned, and the database of working and design drawings of two refineries (over 600,000 documents) was digitised. All the information was consolidated within the 3D General Plan, a new engineering data management system providing access to relevant and exhaustive digital data. It will be used to repair, remodel and design new facilities, resulting in time and cost savings, as well as improving the quality of this work.
The shared services centre (SSC) is a project that demonstrates the need to transform not only production facilities but also back office operations. The SSC will be used to transform accounting and tax reporting, treasury, HR management, and administrative and documentary support processes.
Automation of day-to-day processes will help to free up employees and direct their potential in a more efficient manner. In addition, SSC provides instant access to such information as liquidity, personnel turnover and more.
During the year, KMG and its subsidiaries continued to implement the project management system (PMS). In particular, we launched the Stage Gate Process and a process for comprehensive feasibility study.
The number of companies implementing project management as a priority increased from six to 20, with the list of key projects also expanded. A process was conducted to establish project teams for key projects. We approved methodological documents for our Corporate Project Management System, as well as expert review and risk management guidelines. Finally, we held management training sessions and certification of project managers, and organised a basic project management course for employees of the corporate centre, subsidiaries and associates.
In the coming period, the transformation will be focused on promoting digital technologies in exploration (seismic survey and well analysis) using machine learning and artificial intelligence, as well as on creating a corporate template for new assets digitalisation (a “digital twin”).
Other digital transformation priorities are the environment, occupational health and safety, process reliability, and cost reduction. Particular attention will be paid to improving the digital literacy of KMG employees and young talent as part of the Zhas Orken and Digital Summer internship and apprenticeship programmes.