Occupational health and safety
JSC NC KazMunayGas and its subsidiaries and associates establish that the life and health of employees have priority over the results of production activities and prevention of hazardous production factors in the field of occupational health and safety.
KMG’s Occupational Health and Safety Policy is driven by our senior management setting the tone at the top in occupational health and safety and engaging every employee in building a robust safety culture. Management teams at KMG and its subsidiaries and associates take a zero tolerance approach to losses and damage caused by accidents (including traffic accidents), emergencies, as well as by the use of alcohol, narcotic drugs, psychotropic substances or their analogues. KMG is committed to ensuring compliance with both national laws and relevant international and national standards. The Company will continue to work to ensure a high level of production safety in accordance with global standards and best practices.
2021 highlights
As an industry leader in Kazakhstan, KMG places a strong emphasis on health and safety of its employees and local communities across its footprint. According to our employees, the Company creates safe working conditions and complies with the highest standards to ensure health and safety at the workplace.
In 2021, the number of work-related accidents decreased by 7% year-on-year (from 30 accidents in 2020 to 28 in 2021), with the number of injuries at last year’s level.
In 2021, there was one fatal work-related accident where three employees died (as a result of a fire at Petromidia Refinery, Romania).
The number of road accidents increased by 57% (from 14 accidents in 2020 to 22 in 2021), and the number of fires remained the same as last year, i.e. six.
Unit | 2019 | 2020 | 2021 | Change 2021/2020 | % | |
---|---|---|---|---|---|---|
Accidents | Acc. | 39 | 30 | 28 | -2 | -7 |
Number of injuries | People | 46 | 32 | 32 | 0 | - |
Road accidents | Acc. | 36 | 14 | 22 | +8 | 57 |
Fires | Acc. | 9 | 6 | 6 | - | - |
Unit | 2019 | 2020 | 2021 | Change 2021/2020 | % |
---|
Indicator | 2019 | 2020 | 2021 | |
---|---|---|---|---|
Lost Time Incident Rate (LTIR), per mln person-hours | 0.31 | 0.29 | 0.34 | 0.20 |
Fatal Accident Rate (FAR), per 100 mln person-hours | 2.93 | 0.0 | 1.48 | 0.56 |
Indicator | 2019 | 2020 | 2021 | |
---|
Process safety management
Since 2021, the Company has been gradually implementing the Process Safety Management System (PSM) at KMG’s production facilities to prevent major catastrophic accidents from happening (emergencies, incidents, fires, and accidents), including:
- maintaining the integrity of assets and process equipment;
- establishing safe operating rules, regulations, and procedures in accordance with the statutory requirements of the Republic of Kazakhstan, industry standards, and international best practices and approaches in the field of process safety management (IOGP, OSHA);
- identification of process risks and application of appropriate measures to prevent and mitigate them;
- avoiding damage and losses related to the life and health of the Company’s employees and the public, environmental, financial and legal consequences, property and assets, reputation and image.
The company is confident that the combination of engineering and management elements is effective and seeks to prevent any major catastrophic accidents involving the loss of process equipment containment and, as a consequence, the collapse of structures, explosions, fires, destructive emissions and spills of hazardous substances (chemicals, oil, and oil products). Those engineering and management elements exceed the requirements for workplace safety management because they have an impact on people, property, and the environment.
The Company uses key performance indicators (KPIs) to monitor and analyse the Process Safety Management System:
- lag indicators that allow tracking and recording the actual integrity, system failures, and the number of incidents;
- lead indicators that systematically measure the indicators allowing to assess the performance of the protective and control systems and mechanisms making up the barriers.
Transport safety
In terms of road accident statistics, it should be noted that there are risk factors for accidents that are beyond control of the Company. One such factor is a large number of vehicles – more than 11,000 across the Company. The second factor is the geography of the Company’s subsidiaries scattered across the Republic of Kazakhstan, as well as their location in cities and towns where there is a high risk of road accidents due to the fault of a third party. For example, 41% of the 22 road accidents that occurred in 2021 were caused by third parties.
To reduce the risk of road accidents, the Company implemented the following set of measures to ensure transport safety.
- As part of the safe operation of vehicles as well as to preserve the life and health of the Company’s employees, recommendations were sent under the Road Accident Prevention Action Plan for Subsidiaries.
- Training courses were held for drivers according to a schedule, with testing their knowledge of the Road Traffic Rules of the Republic of Kazakhstan and the updated corporate documents of the Policy and Regulations for the Safe Operation of Land Vehicles of the Company.
- To raise the transport safety level for the Company and its contractors, a preventive event, the Safety Belt, was held in March 2021.
- For outreach purposes and to raise awareness among the employees of the Company and its subsidiaries and to promote the safe driving culture, a video clip was shot in September 2021 on the topic of: “Safe Driving of Motor Vehicles”.
- In connection with the beginning of the autumn-winter period and a high risk associated with the seasonal increase in road accidents, preventive events, Safe Traffic in Winter, were held in November 2021.
- A pilot project, Trip Management, was implemented by Embamunaigas.
In 2022, it is also planned to prepare and train coaches from among the Company’s employees (transport/traffic safety engineers) under the Defensive Driving programme for international accreditation by OPITO, ROSPA, etc.
Fire safety
Six fires occurred in KMG Group in 2021 (just as in 2020), including two large fires with fatalities (three dead and one injured) and significant property damage.
Based on the results of the inquiry into the circumstances and causes of the fires, the following main systemic causes were identified:
- poor commitment and leadership of senior management and line managers;
- low level of safety culture and competence of managers / employees in charge;
- insufficient funding for industrial and fire safety measures;
- inadequate risk assessment and management of “barriers”;
- poor quality of training sessions on people evacuation in case of fire in dormitories and shift camps.
To prevent and avoid fires and ignitions, the Company has taken the following preventive measures to ensure fire safety:
- After large fires, the implementation of Measures to Prevent and Avoid Fires for the Company was immediately requested, with particular attention paid to fire fighting tactics and drills both at production facilities and in shift camps.
- Based on analysing the reports submitted by subsidiaries, random inspections were carried out in November and December 2021 to prevent and avoid fires in dormitories and shift camps across all business lines of the Company.
- To strengthen control over compliance with fire safety requirements and improve the Company’s preparedness to promptly respond to and eliminate fires, the Integrated Action Plan for 2022–2024 was developed and approved, providing for short-term, medium-term, and long-term measures as well as preventive measures to ensure fire safety at the Company’s facilities.
- The Rules for inspection and assessment of KMG Group’s entities’ preparedness to prevent and extinguish fires have been updated and re-approved with reference to Kazakhstan’s statutory fire safety requirements, the KMG Group HSE Management System Guidelines, international standards, and IOGP recommendations.
- For the purpose of fire-fighting outreach and increasing staff awareness, a fire safety handbook for employees and visitors was developed, and a fire safety month was held at the Company’s offices from 4 October to 4 November 2021.
- To reduce the risks of fires and ignitions during the New Year holidays and long weekends, a letter was sent to all business segments of the Company in December 2021, requiring that additional measures be taken to ensure compliance with the fire and electrical safety requirements both at production facilities and in shift camps.
The following initiatives are planned for 2022 to improve the Company’s industrial and fire safety:
- implementing new HAZOP analysis approaches engaging a third-party specialist company at Rompetrol;
- conducting a comprehensive risk assessment to identify potentially hazardous facilities and equipment by using the Risk Based Inspection (RBI) method with the support of JSC Samruk-Kazyna;
- developing a reference manual on the basics of Process Safety / Barrier Management as part of support provided to the Company’s entities;
- implementing short-term measures under the Integrated Fire Safety Action Plan for 2022–2024 approved by the Chairman of the Company’s Management Board;
- checking and evaluating the preparedness of non-state firefighting services to prevent and extinguish fires at the Company’s facilities as part of the Contractor Management process.
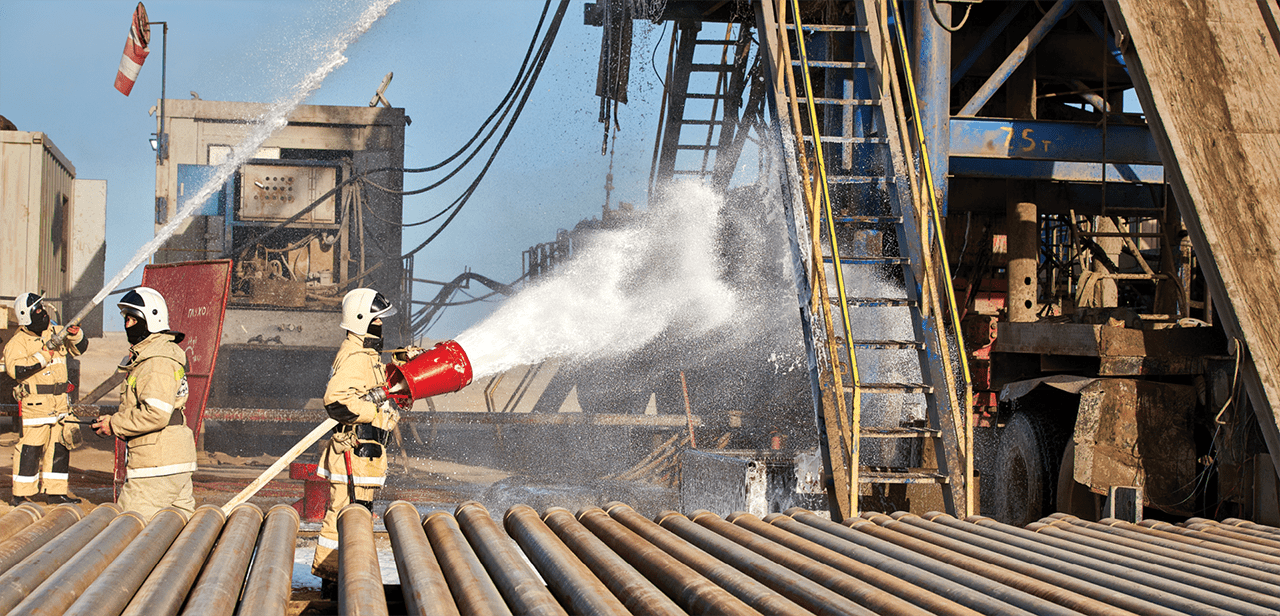
Digitisation of HSE processes
The Trip Management project was initiated to improve transport safety, foster a safe driving culture, and establish a single centralised digital platform, which is being piloted at JSC Embamunaigas.
The project aims to improve road safety through instilling a safe driving culture based on global best practice, advanced digital solutions, and process automation. The project will also unify the trip safety management requirements for all ground transport operations, implement a centralised tracking of key metrics, and enable improved fleet utilisation through analytical reports and corporate-level indicators.
Embamunaigas’ facilities completed the implementation of stage I of the project, with a unified monitoring system for motor vehicles implemented. Stage II planned for Q1 2022 involves functionality expansion in terms of “monitoring deviation from the route” and connection to a unified monitoring system for contractors’ companies.
In 2022, it is planned to replicate the Trip Management project aiming to improve the transport safety condition, reduce road accidents, ensure smart scheduling and accounting, and monitor the efficiency and intended use of vehicles, fuel, and lubricants.
Improving the HSE management system
To protect the life and health of employees during the operation and maintenance of land vehicles, to prevent road accidents and reduce their severity, the JSC NC KazMunayGas Policy for Safe Operation of Land Vehicles was updated and approved, as were the JSC NC “KazMunayGas Group Regulations for Safe Operation of Land Vehicles. All subsidiaries and associates initiated and approved a similar Policy and Regulations for Safe Operation of Land Vehicles. Also, the requirements of that Policy and those Regulations were explained and communicated to all employees via email and/or at briefings.
Corporate Standard was developed and approved for engaging contractors on occupational health, industrial safety, and environmental protection at JSC NC KazMunayGas Group.
JSC NC KazMunayGas’ Occupational Health and Safety Policy was developed and approved.
JSC NC KazMunayGas’ Operating Instruction on Fire Safety in Office Buildings was developed.
In order to evaluate, analyse, and mitigate the industrial safety, occupational health, and environmental protection risks of JSC NC KazMunayGas Group’s contractors, quarterly reports are put together and submitted to KMG’s board of directors with respect to contractors’ HSE breaches, including a summary of penalties imposed.
Fires and significant HSE incidents are promptly reported to the Board of Directors of JSC NC KazMunayGas.
Upon completion of investigation, relevant materials, including an investigation report specifying immediate and root causes and financial damage, copies of orders on disciplinary actions against employees guilty of the incident, as well as documents specifying post-investigation changes and documents aimed at preventing similar incidents in the future, are submitted to KMG’s Board of Directors.
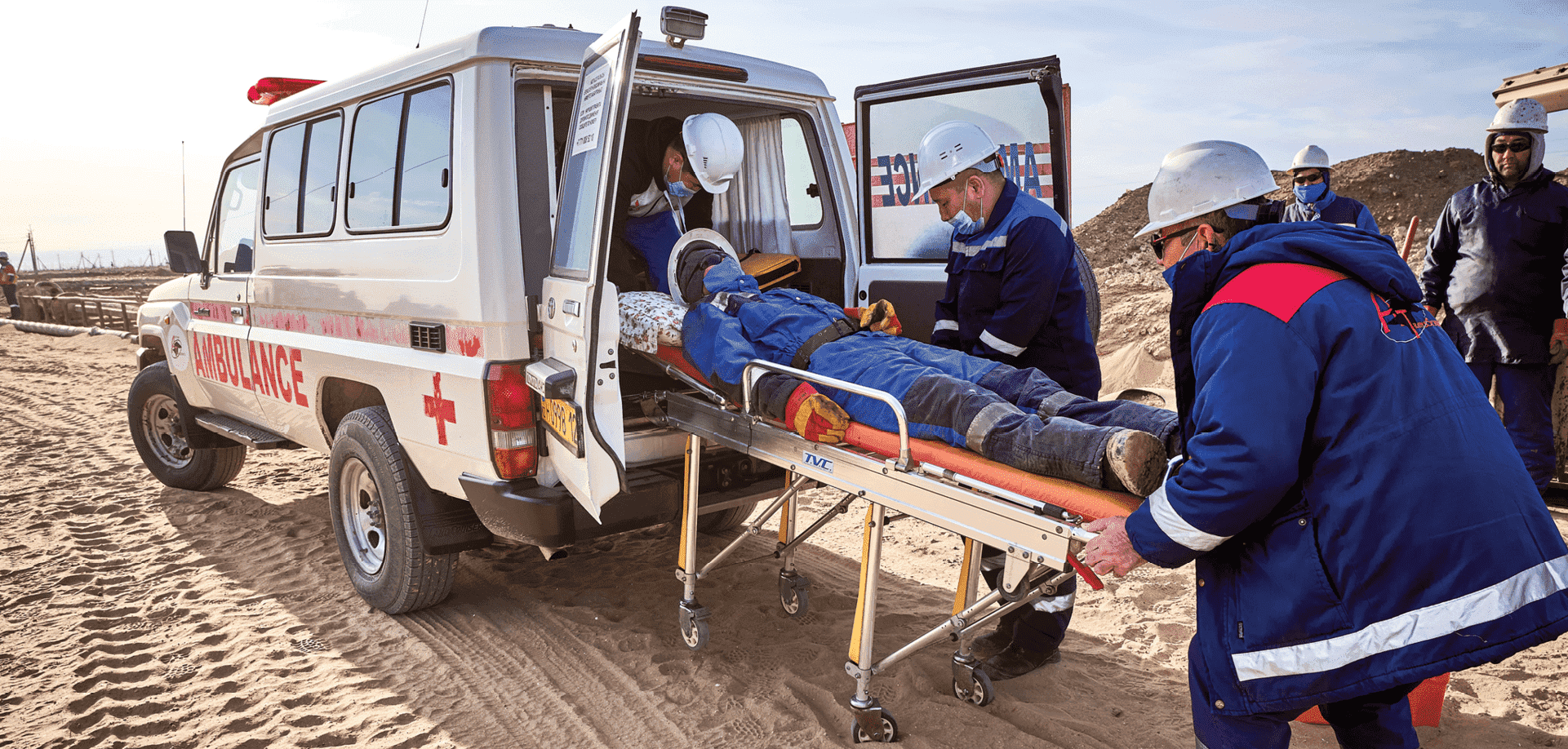
Occupational health and hygiene
The Company manages occupational health and hygiene matters in accordance with the requirements of Kazakh laws and international occupational health standards. KMG is strongly focused on employee health protection and improvement, irrespective of the specific production process involved.
The number of non-injury related fatalities among employees of subsidiaries and associates increased by seven incidents, or 87.5%, year-on-year. Most of the increase in those figures was due to cardiovascular diseases and complications from the coronavirus infection.
In December 2021, training in cardiopulmonary resuscitation was organised for the staff of the KMG CC. Fifteen employees took the Basic Course in Cardiopulmonary Resuscitation (BLS) offered by AIMED International Professional Development Centre LLP.
As part of the Roadmap to improve the efficiency of employee health management within KMG Group, a working group was set up in June 2021, with two medical experts engaged. To implement the Roadmap, the medical care for KMG Group’s employees was analysed, with a visit to the following subsidiaries and associates: Kazgermunaigas, Embamunaigas, KazTransOil, Atyrau Refinery, Kazakhhoil Aktobe, and KazakhTurkMunay. Efforts were taken to develop the Staff Health Management Programme. The programme was included in the KMG Strategy for 2022–2031, which will focus on three main areas: combating the pandemic and its consequences, prevention of occupational diseases, and raising awareness and motivation of employees of or to a healthy lifestyle. Currently, it is undergoing approval by relevant Departments of KMG Group.
In accordance with the approved Plan, the following activities were carried out in 2021:
- employees responsible for occupational health and safety were appointed in subsidiaries and associates;
- measures were stepped up regarding pre-shift health monitoring of workers and their admission to work;
- control of compliance with the dynamic observation of employees with chronic cardiovascular diseases (CVDs) by a serving medical organisation;
- medical workers at medical stations are equipped with all the necessary equipment to conduct a pre-shift medical examination;
- working conditions and risks are assessed to determine the age group of workers at risk, with measures taken to reduce the effect of hazardous and harmful production factors on the health of workers;
- measures were stepped up for primary prevention of CVDs, including both therapeutic measures during disease exacerbation and therapeutic measures to prevent them.
KMG’s efforts are mainly focused on improving the quality of medical services provided by specialised organisations as part of their contractual obligations, including mandatory preliminary (upon entering employment) and periodic medical examinations (health check-ups) of employees engaged in heavy work and work in a harmful and hazardous environment.
There were no cases of occupational diseases in KMG Group.
Progress and ongoing initiatives on preventing the spread of COVID-19
With the onset of the COVID-19 pandemic, KMG Group has amassed useful experience in combating the coronavirus. At the same time, no production processes have ever been stopped throughout the entire period of the pandemic.
Since the start of the pandemic, as of 31 December 2021, there were 5,972 cases of the COVID-19 infection (including cases of the COVID pneumonia without laboratory confirmation) and 119 deaths resulting from the coronavirus and pneumonia registered among the group’s workers (96 in 2020 / 23 in 2021).
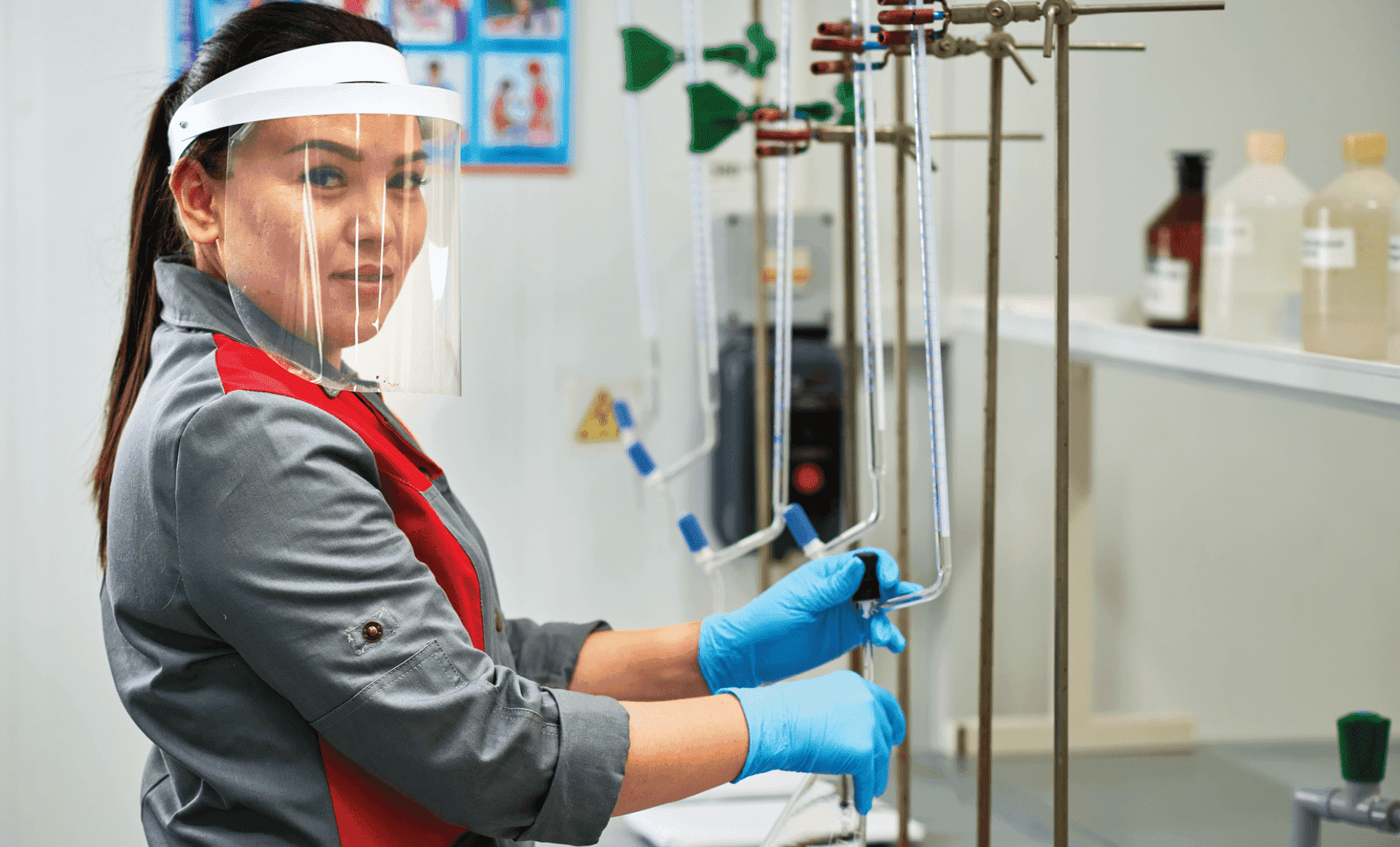
To prevent the disease and minimise the spread of COVID-19, as well as to reduce the impact on production processes, the group takes all the necessary organisational steps and appropriate comprehensive measures to counter the pandemic, including:
- The crisis management team at KMG’s Corporate Centre and the emergency response teams at KMG’s subsidiaries continuously monitor and control the situation and make the necessary management decisions to prevent the spread of the coronavirus by using COVID-19 response protocols, with plans also developed to ensure business continuity and business process recovery
- Before shift rotation, all rotating staff and contractors are lab tested for COVID-19, with arrangements made for the mass testing of employees of subsidiaries and associates, raising awareness of the disease danger and staying alert amid the pandemic
- Restrictions on mass events continue to be in force
- Personal protective equipment and disinfectants are provided in required quantities for the protection of people and disinfection of spaces
- Protocols to be followed if infection is suspected or detected have been implemented. All employees have been advised of the need to promptly report positive test results and their first coronavirus symptoms upon discovery as well as of the liability for withholding such facts, test falsification, or quarantine breach
- To prevent COVID-19 and comply with anti-epidemic rules, regular awareness raising activities are ongoing for employees on prevention (use of antiseptics, masks, social distance, and temperature measurement), disinfection, sanitation, and hygien
- In the event of disease outbreaks among employees, lock-down restrictions are imposed, with workforce reduction at operating facilities or back-up crews involved in operations, and, to the extent possible, personnel are switched to working remotely.
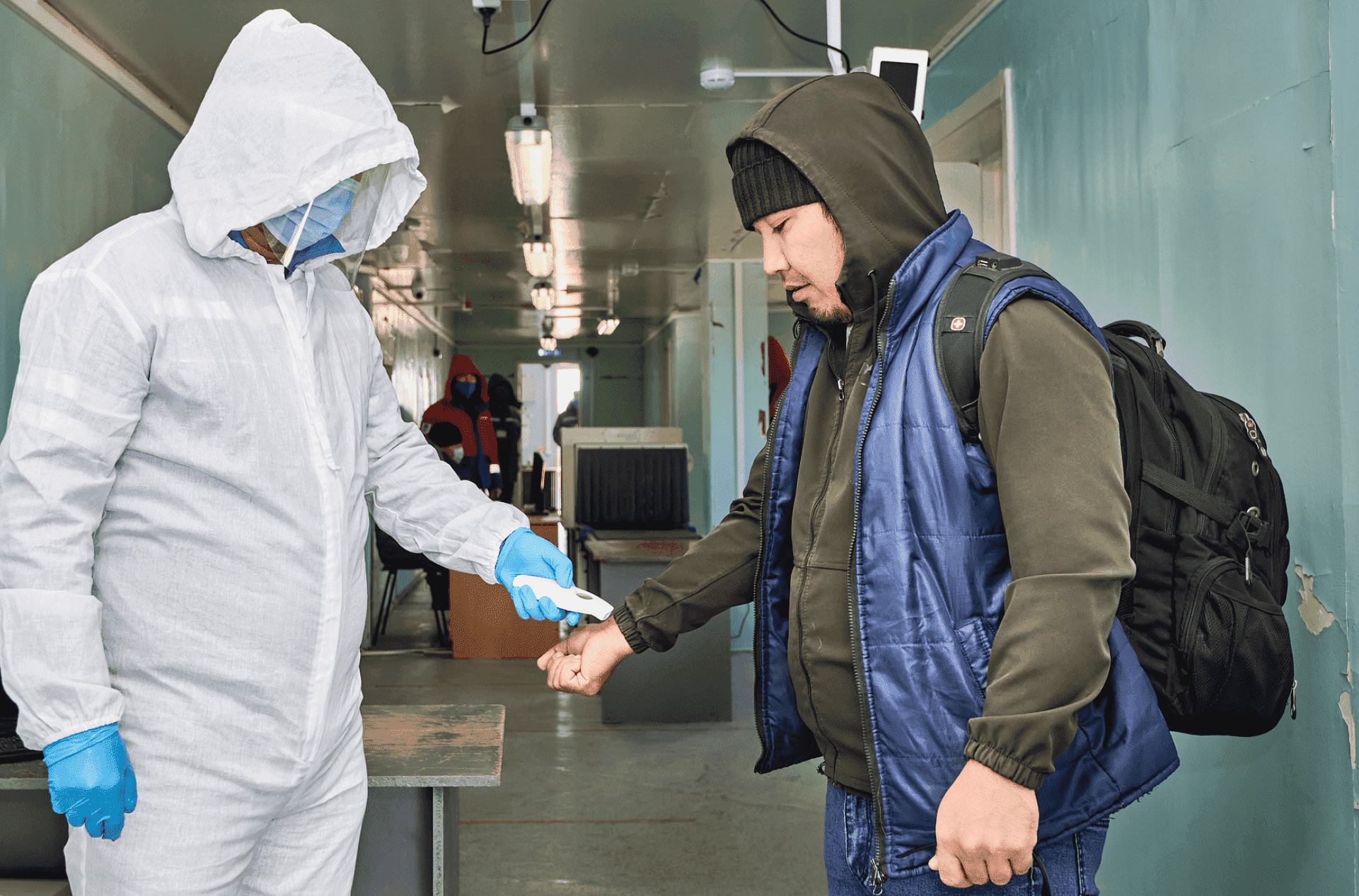
In general, a range of preventive measures and strict disinfection and sanitary protocols are still in place across KMG Group’s operations in accordance with the established anti-epidemic regulations.
Since the start of the state vaccination campaign, action plans have been implemented to organise and encourage vaccination of employees, whereby strenuous awareness-building efforts are being taken to explain the importance of vaccination for collective immunity and ensure the stable continuous operation of the Group’s production facilities.
KMG Group’s employees are vaccinated in outpatient clinics at their place of residence and at private medical institutions. KMG’s operations have all the conditions necessary for that purpose, with vaccination stations organised in the central offices, in dedicated points at the fields, and in medical centres.
For the most part, employees have a positive attitude toward the vaccination campaign and actively participate in it. When each of the two components is received, all employees get two paid days-off.
At the same time, according to the current regulations of sanitary doctors, workers who have received both components of the vaccine have unimpeded access to the fields without taking PCR tests.
As of 31 December 2021, 50,000 employees (76% of the total headcount) were vaccinated across the Group, of which 48,000 (73%) had received a complete course of vaccination (both components).
Also, in subsidiaries and associates as well as in KMG’s administration building, employees use the Ashyq application to enter. The corporate centre has successfully integrated the access control system (ACS) with the Ashyq information system (access with the “red” or “yellow” status is automatically blocked by the ACS, and when the status changes to “green” or “blue”, access is restored).
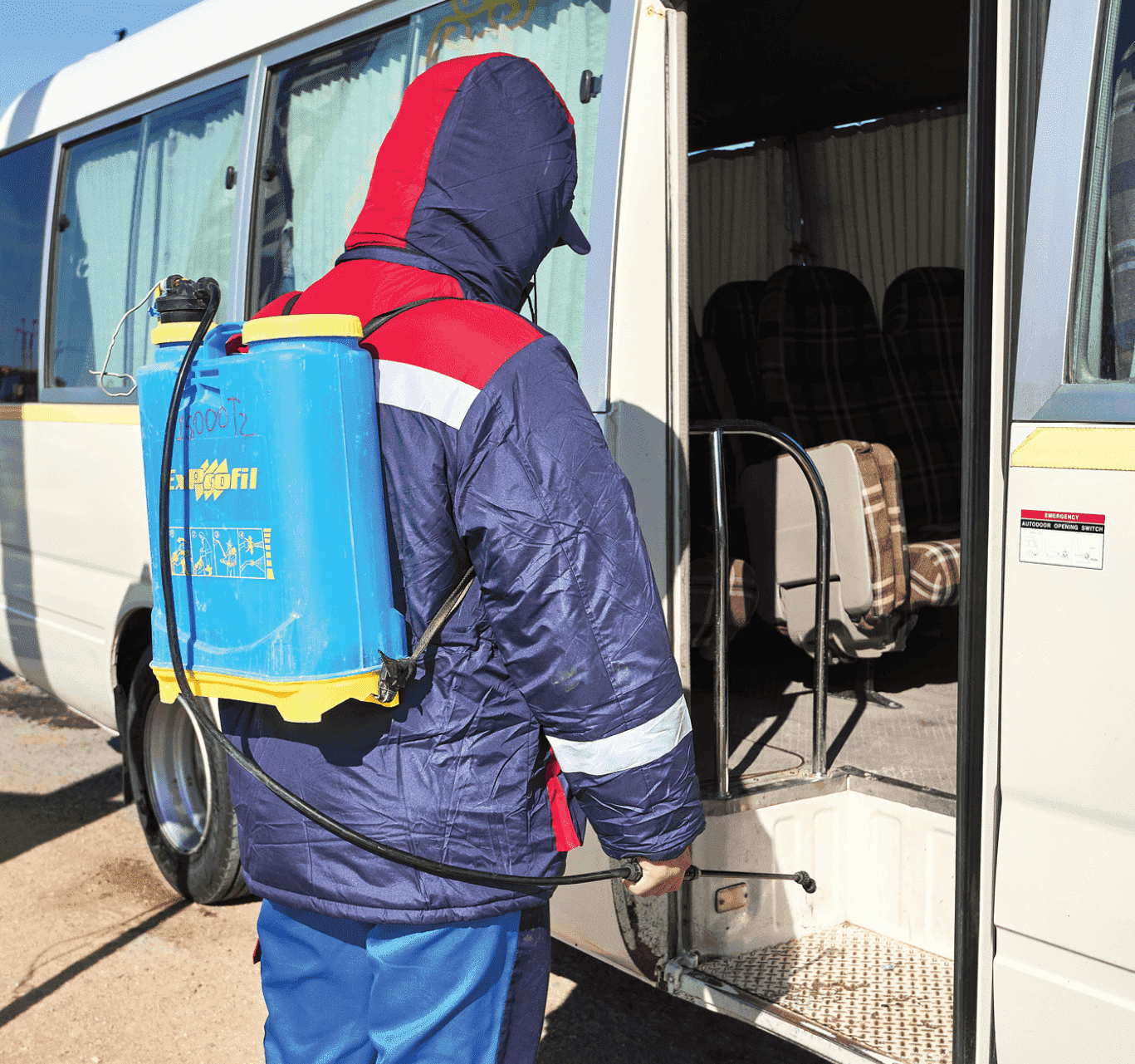
1 Available data on the International Association of Oil & Gas Producers (IOGP) performance indicators for 2020.
1 Available data on the International Association of Oil & Gas Producers (IOGP) performance indicators for 2020.